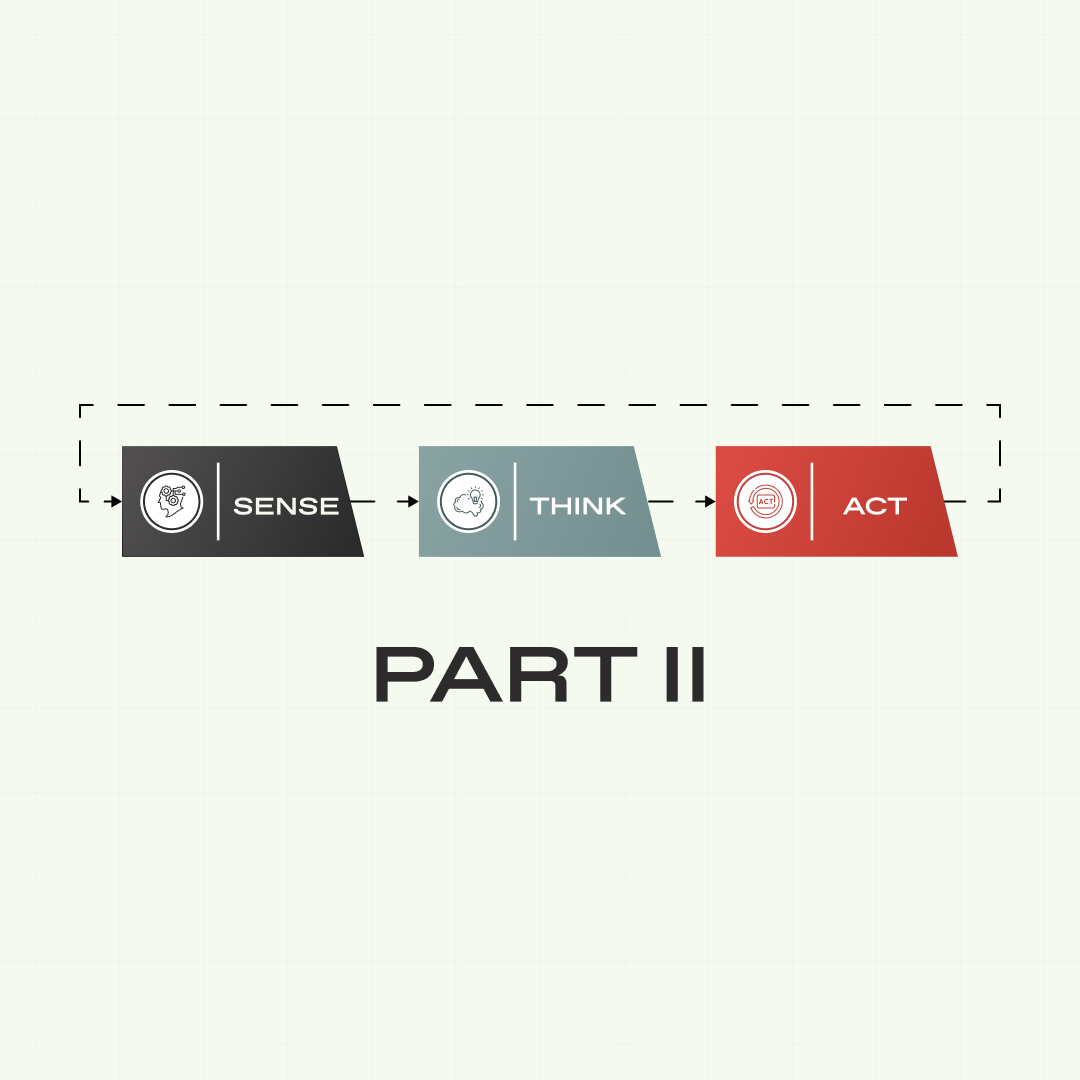
By Camila Key Saruhashi and Leland Chamlin
In Part 1, we explored how AI is transforming foundational industries by redefining the Sense-Think-Act framework — where AI systems sense real-time data, think by analyzing and making decisions, and act autonomously to optimize industrial operations. This integration is paving the way for fully autonomous, AI-driven systems that enhance productivity, efficiency, and resilience.
Now, in Part 2, we shift our focus to the Factory of the Future — a fully AI-native ecosystem where humans, AI agents, and adaptive machines collaborate seamlessly. We’ll explore how AI is redefining the roles of humans and machines and the challenges companies must overcome to build and scale AI-powered industrial systems.
The Future Factory: AI-Driven Manufacturing
The Factory of the Future will be an intelligent system where AI agents orchestrate operations, humans drive strategy, and machines execute dynamic tasks autonomously. This transformation won’t happen overnight — it requires foundational building blocks, including AI integration, real-time data infrastructure, and adaptive automation.
- Today – AI enhances human decision-making and automates discrete tasks.
- Near Future – AI agents coordinate workflows, optimizing production in real time.
- Long-Term Vision – Factories become self-optimizing ecosystems, with AI making autonomous decisions and humans focused on strategy.
Key Roles in the AI-Powered Factory
Humans: Strategic Oversight & Innovation
As AI takes on more operational tasks, human expertise will remain essential in areas that require judgment, creativity, and strategic direction:
- Goal Setting – Defining objectives, guardrails, and key performance indicators (KPIs) for AI systems.
- Oversight & Governance – Ensuring AI decisions align with business goals while preventing biases or errors.
- AI Training & Model Validation – Providing domain expertise to fine-tune AI algorithms and validate outputs.
- Exception Handling – Managing edge cases and unforeseen scenarios that require human judgment.
AI Agents: Intelligent Orchestration
AI agents will serve as the brain of modern manufacturing, seamlessly integrating humans, machines, and data into a fully intelligent ecosystem. Their key functions include:
- Real-Time Optimization – Continuously monitoring machine performance and adjusting operations instantly to maximize yield, throughput, and energy efficiency.
- Closed-Loop Control – Establishing adaptive feedback loops between machines and robots, enabling self-correction and continuous learning for improved precision and reliability.
- Human Collaboration – Translating complex data into plain-language insights through chat, voice, or visual dashboards, guiding operators, and coordinating multi-agent workflows.
Machines & Robots: Precision Execution
Machines and robots are evolving from static, pre-programmed tools into adaptive, AI-driven systems capable of real-time decision-making and dynamic execution. Key advancements include:
- Modern AI-Guided Machines: Dynamically adjust temperature, pressure, speed, and other parameters based on sensor data and feedback loops, optimizing performance with minimal human intervention.
- General-Purpose Robots: AI-powered robots capable of handling assembly, inspection, transportation, and data collection, adapting to diverse tasks with minimal reconfiguration.
The Opportunity: The Rise of AI-Native Manufacturing
A next-generation manufacturing model is emerging — one that moves beyond individual components to fully integrated, AI-native production systems. Instead of selling modular software, companies are developing end-to-end manufacturing platforms that seamlessly unify hardware, middleware, and applications into a single, AI-driven system.
This approach challenges the traditional software-vendor model and is built on a core belief: AI will revolutionize manufacturing only when built in-house — where the same entity controls software, operations, and production.
By maintaining a tight feedback loop between AI systems, real-world operations, and business goals, these companies achieve a level of automation, efficiency, and adaptability that modular solutions cannot match. One example is Hadrian, a Construct portfolio company, which is pioneering the Factory of the Future for defense and aerospace, demonstrating the potential of this AI-first industrial model.
Challenges and How to Win
Building AI-driven manufacturing solutions requires overcoming significant hurdles in data integration, stakeholder alignment, and enterprise adoption.
1. Data Integration & Quality
Manufacturing environments rely on a mix of legacy and modern systems, making seamless data integration a challenge. Converting physical operations into reliable digital data is further complicated by hardware malfunctions, programming errors, and data misalignment, which create information gaps. Additionally, manufacturers operate with a "trust but verify" mindset, demanding near-perfect reliability before scaling AI-driven solutions.
2. Stakeholder Complexity
Adopting AI in manufacturing requires aligning diverse priorities across an organization. Operators and engineers prioritize uptime and safety, data teams focus on scalable and contextualized data pipelines, and executives need analytics and scenario planning tools that tie AI to business outcomes. Addressing these competing needs is crucial to gaining traction and ensuring broad adoption.
3. Pilot Purgatory & Long Sales Cycles
Even when a solution meets technical and organizational requirements, scaling remains a challenge. Many pilots stall in the "valley of death," with enterprises taking 12–24 months to move from evaluation to full rollout. Winning companies will break this cycle by demonstrating early, measurable ROI, minimizing integration complexity, and building scalable architectures that evolve with customer needs.
Who Will Win?
The winners in AI-driven manufacturing will be those who tailor their approach based on the market they serve:
1. Ground-Up Builders for Fragmented Markets
In fragmented industries where small, outdated facilities dominate, success will come from starting fresh. Companies that fully control operations can build AI-native factories from the ground up, designed with modern principles from day one. Example: Hadrian is disrupting precision manufacturing by replacing legacy machine shops with AI-optimized factories, mirroring how Uber leveraged mobile-first platforms to disrupt transportation.
2. Horizontal Optimizers for Incumbent Markets
In markets dominated by large incumbents, the winning strategy is to layer AI-driven optimization onto existing infrastructure. These enterprises have already invested in automation — their focus is on extracting more value from their data, reducing labor costs, and enhancing efficiency through AI-powered orchestration.
Both strategies recognize the physical constraints of manufacturing and the importance of tight feedback loops between shop floors, data systems, and management. The right strategy depends on the market—whether replacing outdated infrastructure or optimizing legacy systems.
Final Thoughts
AI isn’t just an evolution — it’s a revolution in manufacturing. The companies harnessing AI today are laying the foundation for the smart factories of tomorrow — factories that are more resilient, efficient, and sustainable.
AI’s impact has expanded far beyond software. It now touches everything: infrastructure, overhead, labor — every operational dollar that keeps foundational industries running. It’s a step-change in how we think about market opportunity. We’ve moved from targeting software spend to capturing the full operational spend of industries that drive half the GDP.
The companies that recognize this shift — those who can bridge AI, automation, and industrial execution — will define the next era of manufacturing.
If you’re building in this space, we’d love to hear from you.